Peiseler rotary indexing tables form the centre of a rotary indexing machine with various processing stations and a loading and unloading station. One particular requirement for our design is the need to achieve a maximum power density for highly dynamic indexing times in the smallest possible installation space.
Largest multi-axis combination in 200-year history increases productivity in manufacture of lightweight components
Remscheid, 4 February 2021 – A Peiseler rotary indexing table is helping a well-known German automotive manufacturer to boost its productivity. The Remscheid company developed the innovation in partnership with customer UNIOR machine tools in Slovenia. The rotary indexing table is the heart of a machine tool produced at the site, which will ultimately be used to machine lightweight components for the production of electric cars. "The table measures 3000 millimetres in diameter and weighs ten tonnes", explains Marc Gronau, Sales Manager at Peiseler. "This makes it the largest and most sophisticated unit of this type that we've created in our 200-year history as a company".
The unit is based on the worm-gear-driven Peiseler ATU 1600 rotary table, which uses a direct path measurement system to move six ZATC 300 two-axis rotary tilt tables between machining stations in five stages, before retracing back to the starting position. The rotary indexing table is equipped with a total of 13 axes and has a maximum load of 250 kilograms per station. These axes guarantee high-precision simultaneous workpiece processing.
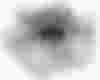
Basic table: Configurable drive concept
Precision mechanical engineering
The Peiseler rotary indexing table is at the heart of the rotary indexing machine, which has five stations for drilling and milling processes plus a loading and unloading station. "The key requirements for our design went beyond the need to achieve a maximum power density for highly dynamic indexing times in the smallest possible installation space", says Gronau. "In order to minimise the tolerances present, we had to position each of the two-axis rotary tilt tables as precisely as possible, both as standalone units and in relation to one another". Providing the media required to close, release and monitor the workpiece clamping device was also a complex task. A rotary manifold with eight ports was ultimately fitted for this purpose.
"This rotary indexing table is not only the largest we've built to date, but also a customer-specific solution that will shorten cycle times and reduce unit costs in the production of electric vehicle components", explains Gronau. As a high-precision manufacturer of trunnion tables, rotary tables, two-axis rotary tilt tables, swivel heads and workpiece changing tables, Peiseler is helping to build the reliable production processes that will lay the foundations for our future mobility.
Core components: Two-axis rotary tilt table
Used serie(s)